Compass Technology Group specializes in characterizing microwave materials, and our approach to solving our customers’ complex problems is ‘Innovation’.
We are a collection of scientists, engineers, integrators, designers, technicians, developers, builders, organizers and leaders. We revel in solving our customer’s hardest measurement problems, and we approach every challenge with both inside and outside-of-the-box thinking. We think big while paying attention to the details.
This comprehensive approach to problem solving has served us well and we are a pioneer in the development of novel technologies for materials measurement. Below are some examples of our innovations…
Success Stories
Surface traveling waves consist of electromagnetic energy where the propagation of that energy is exactly parallel or grazing to the plane of the surface. This is in contrast to the phenomena of specular reflection, where incident energy is at some other angle besides grazing and the surface than reflects the incident energy into a complimentary angle determined by Snell’s law. While sensors exist to determine specular performance on aircraft, currently a useful field inspection capability to assess coating performance for traveling wave does not. Compass Technology Group (CTG) proposes to develop a new concept in microwave nondestructive evaluation (NDE) of specialized coatings in support of the Air Force’s requirement for in-situ microwave traveling wave testing. The offered design specifically addresses the need for high-fidelity measurements of aircraft surface coatings in a field environment and is based on a wide-band probe technology that can operate over the whole 2 to 18 GHz range. Additionally, the proposed concept is conducive to being compact and lightweight.
Compass Technology Group (CTG) proposes to develop a new concept in microwave nondestructive evaluation (NDE) in support of the Air Force’s requirement for transparent conductive canopy coating testing. The offered design specifically addresses the need for high-fidelity measurements of defects in aircraft windows in both manufacturing and in-service (depot and field) environments. This recommended concept can be easily automated while still providing improved sensitivity over a broad frequency range when compared to existing measurement methods. The research program will investigate a modified free-space method that leverages recent near-field probe and free-space materials measurement technology. Full-wave computational modeling will be used to refine the measurement architecture during phase I, and computational-based antenna optimization methods will be used to design the probe configuration to maximize both bandwidth and probe efficiency. Unlike recent resonant probe designs, the proposed CTG solution uses wide-band antenna technology for optimal sensitivity without sacrificing bandwidth. Additionally, the proposed common architecture will be ideally suited for use in both manufacturing environments where quality assurance measurements are needed, as well as in depot or field environments (e.g. on installed cockpit canopies) where installed performance and damage assessment is the desired quantity.
Aircraft transparency systems such as canopies incorporate conductive layers that provide electromagnetic interference (EMI) shielding. These conductive layers require inspection during manufacturing and throughout the life of the aircraft to ensure proper electrical performance is achieved and maintained. Current manufacturing inspections are conducted manually, are time consuming, and do not cover 100% of the transparency surface. Compass Technology Group (CTG) proposes an expanded Phase II effort to develop and demonstrate a new concept in microwave nondestructive evaluation (NDE) in support of the Air Force’s requirement for transparent conductive canopy coating testing. The offered design specifically addresses the need for high-fidelity measurements of defects and manufacturing variations in aircraft windows in both factory and in-service (depot and field) environments. This recommended concept is easily automated while still providing improved sensitivity over a broad frequency range when compared to existing measurement methods, the proposed Phase II program not only develops the measurement concept but also includes advanced development of automation of the technology so that it is fully demonstrated in the manufacturing environment by the end of the effort.
Traditional anechoic chamber wall treatments have consisted of geometrically tapered carbon loaded foam, which provides good near-normal incidence absorption of specular energy. While this material has served the testing community well over the last few decades, it is fundamentally limited because of the high level of diffuse scatter (tip diffraction), that increases the overall noise level in a chamber. To reach the reduced noise levels necessary for modern aircraft avionics and antenna testing, a new paradigm in anechoic chamber absorber is needed. The research program outlined in this proposal addresses this need by applying recently developed computational tools and design methodologies for electromagnetic materials. Through full-wave computational design, the material performance will be optimized over the full range of angles and frequencies needed in this application. Unlike traditional pyramidal absorber, the proposed absorber concept has an inherently low amount of diffuse scatter while improving specular performance over the traditional materials. The proposed concept also leverages current materials technologies and manufacturing methods so that anticipated manufacturing costs should be in line with current pyramidal absorber materials.
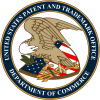
Patents
Various examples of methods and systems are provided for traveling wave spot probes. In one embodiment, among others, a traveling wave spot probe includes one or more antennas positioned proximate to a coated surface. The one or more antennas can be configured to excite a surface traveling wave moving over an area under test by launching radio frequency (RF) energy at approximately a grazing angle to the coated surface under test. The one or more antennas can be positioned on a base placed proximate to the coated surface. The base can define the area of the coated surface under test. In another embodiment, a method for non-destructive testing of a coated surface includes positioning one or more antennas proximate to a coated surface and exciting a surface traveling wave over an area under test by transmitting RF energy via at least a portion of the one or more antennas.
An electromagnetic chamber absorber provided improved absorption across a wideband and both lower diffuse and specular scatter and a method for constructing the same. An exemplary device can compromise a periodic arrangement of disconnected electromagnetically lossy elements where the periodicity of the lattice is adjusted to suppress all or most grating lobe scattering. Because the electromagnetically lossy elements are disconnected, scalable manufacturing approaches are enabled. The lossy elements can be easily fabricated via shaping, which includes rolling, folding and cutting resistive and/or magnetic sheet materials. The lossy elements can be repeatably placed in a periodic lattice using low density scaffolding approaches and/or other alignment mechanisms. The absorption at the lower frequency part of the electromagnetic bands (below 1-2 GHz) can be improved via the addition of parallel lossy sheets into the low-density scaffolding.
Various examples of methods and systems are disclosed for non-contact determination of coating thickness. In one example, among others, a method includes illuminating a surface having a layer of a coating material with electromagnetic (EM) energy transmitted at two or more frequencies, obtaining measured reflection data from reflected EM energy, and matching the measured reflection data to modeled reflection data of a reflection model based upon minimization of an error between the measured reflection data and the modeled reflection data to determine a measured thickness of the layer. In another example, a system includes a probe configured to illuminate an area of the surface including a layer of a coating material with EM energy and receive reflected EM energy, and a processing device configured to determine a measured thickness of the layer based upon minimization of an error between measured reflection data and modeled reflection data.